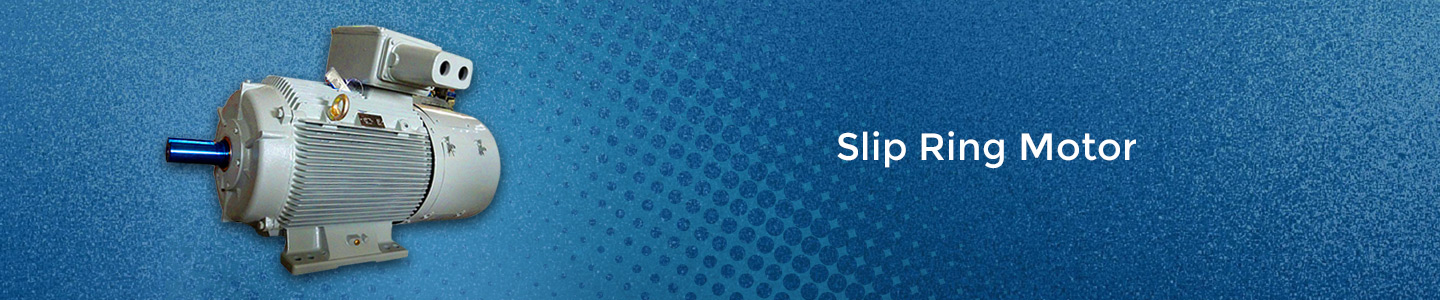
Suppliers, Distributors, and Exporters of Slip Ring Motor
Aakash Power is a Global Supplier, Exporter, and Distributor of Slip Ring Motor, delivering complete motor solutions to the world’s most demanding industries. Our Slip Ring Motors are approved by the international set of standards.
INTRODUCTION
Designed basically for heavy duty use with driven machine imposing overloads and severe mechanical shocks and vibrations. These motors are equally suitable for smooth constant loads since the motors are also designed with high efficiency and power factor. Because of optimum utilisation of materials, with improved ventilation techniques the motors are 10 – 15% lighter in weight and yet more rugged because of their inherent special construction.
Because of high Pull Out Torque and inherent thermal margin kept for high slip operation (with suitable external resistance) these motors are ideally suited for rerolling mills and cane cutter/cane crusher/cane leveller/cane fiborizer applications pertaining to sugar industries. Because of high efficiency and power factor these motors are also suitable for pump/fan compressor applications.
FEATURES
Type | Slipring [squirrel cage range is also available] |
Protection & Cooling | IP23 (Screen Protected Drip Proof), IC01 |
Duties | The motors are basically rated for S1 (continuous duty) but can be adapted to other duties such as S6, S7, S8 etc. |
Insulation | Class ‘F’ insulation (temperature rise limited to class ‘B’) |
Supply | 3 phase, 415 Volt ± 10%, 50 Hz ± 5% as standard. Other voltages and frequencies are also catered 3.3/6.6 kV options are available. |
Slipring and brushgear | Continuously rated |
Winding treatment | Tropicalisation treatment is provided as a standard practice. |
Enclosure treatment | Tropicalisation treatment is provided as a standard practice. |
Mounting | a) Horizontal foot mounted – B3 mounting as standard. b) Vertical flange mounting – V1 construction available |
CONSTRUCTION
Frame and End shields
Girder construction, rugged cast iron/M.S. fabricated frame with internally ribbed heavy cast iron/M.S. fabricated endshields with centering spigots and each secured by high tensile bolts.
The feet with ample thickness, are cast integrally to the frame and access is available for vertical drilling for dowelling pins to obtain positive location and retention of alignment with driven machine under severe mechanical shock, vibration or thermal expansion/ contraction over a period.
Two eye bolts, are provided in stator frame. Each endshield is furnished with steel mesh covered ventilation openings except for force ventilated motors where only two openings for fixing the ventilating ducts are provided. To cater to higher outputs the frames are of fabricated MS construction, having internal ribs.
Stator and Rotor
Cold rolled (non-oriented) steel sheet is used for stator/rotor laminations. Laminations are held by steel endplates.
Stator laminations are keyed and retained in the stator frame through a key ring while the motor laminations are keyed to the shaft and secured by steel endplates.
Stator/Rotor are of CW motors are built up with ducted cores, which ensures radial cooling for more efficient heat dissipation.
Winding
Stator is wound either with dual coated super enamelled wire dual coated with glass fibre lapped enamelled strip conductors, depending on size and application of motor.
Rotors for frame sizes upto RW78 are wound with round superenamelled copper wire whereas for higher sizes bar wave windings are provided.
Rotor coil overhangs are secured to an internal support ring, while upper portion of the overhang is secured with thermosetting resiglass banding.
Insulation/Treatment
Class ‘F’ to IS 1271. Temperature rise limited to class ‘B’ limit in accordance with IS 325. The insulating materials, binders, fillers and impregnants used for Class ‘F’ insulation are the latest and proven to be fully compatible under thermal cycling are ageing, while thicknesses, layers, direct and creepage clearance supporting and securing elements etc. are maintained at a level that only caters to the basic insulation levels governed by the voltage class of the motor but takes care of the mechanical stresses caused by the thermal cycling, short circuit and overloads, overspeeding, frequent starting/braking, forced vibrations, and shocks over the anticipated motor life.
The wound stators and rotors along with their leads are first preheated for expulsion of moisture, cooled to prepolymerisation temperature of the varnish, dipped in thermosetting varnish and baked – the number of dipping and baking cycles depending on the type of environment and service condition.
Ventilation System
A powerful and effective ventilation system furnishes a large safety margin on temperature rise thereby minimising duration for elevated temperature. Additionally specially designed slots are provided in the large frame sizes for direct cooling of stator conductors.
The axial ventilating holes and the specially designed slot system along with the blower capacity and baffle (air guide) system together ensure effective cooling to limit the winding temperature rise to safe value. A high capacity radial discharge shaft mounted blower along with a fixed air guide provides a powerful suction through the motor.
The fan blades are specially designed for minimum windage loss. Air is drawn from the non drive end radially and expelled similarly at the drive end. CW motors are having axial and radial cooling circuit . Stator frame has number of ribs while rotor has spider shaft which allows air to flow and circulate radially.
Balancing
Rotors along with shaft mounted blower are dynamically balanced as per Grade 2.5 to limit vibration to value well within specified limits as per IS:12075. Lower vibration levels when specified by users, may also be provided.
Shaft
Large diameter shaft : For large output the shaft is often moun-ted with 2 bearings at drive/non drive end depending on design.
Bearing/Lubrication
Ball and roller bearings are standard. Cartridge – type housings exclude foreign matter and facilitate easy maintenance. CW motors are designed with spider shafts to facilitate radial cooling system.
The motors are equally suitable for direct coupling through flexible or solid couplings. The ball bearing at non driving end serves as the locating bearing and caters to the axial thrust associated with the most normal drives.
However is case of high magnitude of thrust as in the case of vertically mounted motors, a special bearing arrangement such as duplex or angular contact, is incorporated. The bearings are housed in cartridges which are spigot located accurately into the endshields, thereby furnishing the facility of motor withdrawal from stator without disturbing the bearings.
Bearings for CW motors are mounted directly on the bracket removing the use of cartridge. Regreasing nipples are provided and are fully accessible for grease replenishment when the motor is in service. Bearing cartridges are machine groved to prevent ingress of excess grease into the motor. 'Shekk' Gadus 3 grease in used as standard.
Slipring Unit, Brushes and Brushgear
Sliprings of hard wearing Copper alloy are mounted outside endshield at nondriving end. Collector is keyed to shaft and secured to witstand thermal cycling shock and vibration.
Carbon brushes are of a grade specially selected to provide satisfactory wear life. The brush holders are amply rated, the design of tension spring and associated levers permit only a small change in brush pressure for a large amount of brush wear, thereby minimising the frequency of tension adjustment. All brushes are fully bedded on the collector and run in before the motors are despatched from the works.
Slipring chamber is designed for rapid access to the brushgear and sliprings. Sliprings and brushgears are continuously rated for motors requiring speed regulations (with external rotor resistance) or with freqent starting and stopping.
Slipring chamber is having provision for ventilation for cooler operation. Slipring assembly for higher Rotor Voltages (>1000V) are specially manufactured by providing phase separators.
Terminal Box
Two terminal box seats are furnished on opposite sides of the frame enabling a choice of position (right or left handside) of the terminal box.
All current carrying parts and their associated fastners are sutiably plated. Large size terminal box of fabricated steel are used for easy access. The terminal box is mounted on an adaptor plate. Cable boxes and glands to suit the motor users cable may be provided.
APPLICATION
Designed basically for heavy duty use with driven machine imposing overloads and severe mechanical shocks and vibrations. These motors are equally suitable for smooth constant loads since the motors are also designed with high efficiency and power factor.
Because of optimum utilisation of materials, with improved ventilation techniques the motors are 10 – 15% lighter in weight and yet more rugged because of their inherent special construction.
Because of high Pull Out Torque and inherent thermal margin kept for high slip operation (with suitable external resistance) these motors are ideally suited for rerolling mills and cane cutter/cane crusher/cane leveller/cane fiborizer applications pertaining to sugar industries. Because of high efficiency and power factor these motors are also suitable for pump/fan compressor applications.
KNOWLEDGE BASE & FAQ
A wound-rotor motor is a type of induction motor where the rotor windings are connected through slip rings to external resistances.
Adjusting the resistance allows control of the speed/torque characteristic of the motor.
Typically, slip ring consists of a stationary graphite or metal contact (brush) which rubs on the outside diameter of a rotating metal ring.
As the metal ring turns, the electric current or signal is conducted through the stationary brush to the metal ring making the connection.
A split-ring commutator makes the current change direction every half-rotation, whereas a slip-ring commutator merely maintains a connection between the moving rotor and the stationary stator.
SLIP is the difference between the synchronous speed of the magnetic field and the shaft rotating speed and would be some number of RPM or frequency.
The slip increases with an increasing load, thus providing a greater torque. Speed of the rotor of an induction motor is always less than its synchronous speed.
A split-ring commutator makes the current change direction every half-rotation, whereas a slip-ring commutator merely maintains a connection between the moving rotor and the stationary stator."
Slip refers to the difference between the shaft rotating speed and the magnetic field's synchronous speed, which is measured in frequency or RPM.
The percent slip is a method that helps calculate an electric motor's speed performance. A higher load also increases the slip and the amount of torque produced.
Torque developed by induction motor is proportional to the slip. At synchronous speed, slip is zero and hence torque developed by the motor is zero.
In case of ideal motor having zero friction and zero losses, motor can rotate at synchronous speed, because motor need not develop any torque to sustain rotation.
The complication and maintenance associated with brushes and slip rings is a disadvantage of the wound rotor as compared to the simple squirrel cage rotor.
This motor is suited for starting high inertial loads. A high starting resistance makes the high pull out torque available at zero speed.
Both are the types of Asynchronous machines(Induction Machines), difference is that in Slip ring we can change the starting torque by simply varying the External resistance connected to rotor, this is not possible in case of squirrel cage induction motor.
PRICING
Contact us for more information on Slip Ring Motors or to discuss your requirements. Enquiries are solicited for India, UAE and Africa on following Email id web@aakashpower.com